Post-Processing Strategies in AM
Additive Manufacturing towards Industrial Series Production
Additive manufacturing (AM) enables the production of complex and mass customized parts that are too expensive or even impossible to manufacture using conventional manufacturing processes, such as milling or casting. Therefore, LPBF has the capability for incremental and radical innovations in products and services. However, main challenges in the as-built quality of AM include the adherence to precise geometrical accuracy and high-quality surface roughness.
While AM enables the production of highly complex parts, conventional manufacturing technologies still are the ones that enable high precision. The combination of the two processes thus unlocks the advantages of both. The objective of this research is to develop strategies that combine different production processes under consideration of the entire AM process chain to facilitate and reduce post-processing. The strategies are validated in an end-to-end process chain.
Manufacturing Elements
The geometrical accuracy, a high-quality surface roughness, and high-quality material properties are challenges for the production of AM parts for end-user applications. To increase the capabilities of the AM process and to facilitate post-processing, a promising approach is to tailor process parameters for the fabrication of a part, called the manufacturing elements (ME) approach. However, the approach has not yet been applied to an end-to-end implementation of a real-world case study.
This study examines the application of the manufacturing element approach end-to-end to manufacture a complex-shaped real-world case study and demonstrates its practical applicability. The project was a collaboration with the Paul-Scherrer-Institute and CERN.
Find the publication under the following Link: external pagehttps://doi.org/10.1016/j.addma.2021.102140call_made
Bolt Interfaces
The surface roughness and form deviations of AM parts are high. Therefore, post-processing is required which needs standardized interfaces to avoid customized clamping chucks and manual handling. Broadly applicable AM-integrated clamping interfaces should enable large tool accessibility, no clamping forces are introduced, and robotic part handling is made possible due to defined interfaces for medium and large-sized parts. Especially for complex AM parts, integrated interfaces enable a productive handling and clamping process.
This study introduces the concept of AM-integrated bolts, validate the concept, and demonstrate the practical applicability of the bolts through case studies.
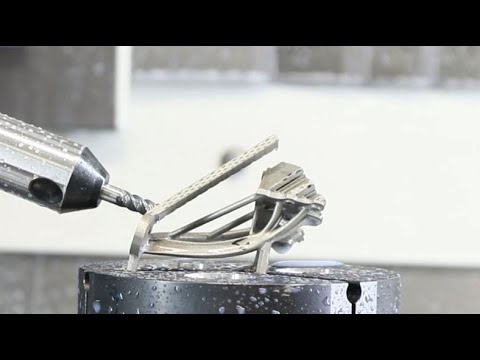
Find the publication under the following Link: external pagehttps://doi.org/10.21203/rs.3.rs-484243/v1call_made
Sheet Metal Interfaces
The clamping and handling of small- and medium-sized complex AM parts are a challenge with currently available clamping systems as the tool accessibility is limited. This strategy utilizes a disposable piece of sheet metal as a removable hybrid substrate plate during the AM process which also serves as a clamping interface for the milling process for AM parts. This sheet metal clamping interface enables large tool accessibility from the top as well as from the bottom of the part. Due to defined interfaces it allows robotic handling of AM parts.
Our current study presents and validates a novel modular clamping system for disposable sheet metal profiles that are used as interfaces for LPBF, handling, and post-processing.
Abrasive Flow Machining (AFM) Model
Internal channels produced by LPBF have rough surfaces and require post-processing, which is difficult due to their very limited accessibility. AFM is a commonly used process for conventionally manufactured parts. The basic principle of AFM is to press an abrasive fluidic medium through channels to smooth the walls. For AM parts, normally several physical test iterations are required to find an appropriate channel design, which can be treated by AFM. The complex flow behavior of the fluidic medium makes it difficult to predict its abrasive effect.
A new model based on pressure and velocity is proposed to simulate complex LPBF-manufactured channels. This model predicts the surface roughness and the thickness of the material removed from the walls of complex internal channels.
This study presents and validates an AFM model to predict the final surface roughness and removal of material from internal channels with a constant diameter.
Find the publication under the following Link: external pagehttp://dx.doi.org/10.1108/RPJ-09-2019-0241call_made